自动制砖设备日常故障问题与处理方法
来源:网络收集 点击: 时间:2024-08-30制品有裂纹现象时
故障分析:
原料过粗、粘性不够、水分失调。处理方法:调整有粘性的原料掌握水分的配比。
底模有毛刺会出现砌块是有刮痕掉角的现象。处理方法:清理模上的毛刺及穿筋上的混凝土。
上模不吐底模会出现砌块贴在上模压脚上。处理方法:调整上模的橡胶垫或增加震动时间。
两侧定位销有一侧定位销没有销注上模会出现减速机坏或卡模现象坏砖现象。处理方法:将上模放入底模后调整两侧定位销。
减速机起模不同时。处理方法:调整减速机摇臂。

上模不入底模
故障分析:
前后顶丝错位。处理方法:调整顶丝间隙,让上模放入底模后调整顶丝间隙应在1—2mm之间。
撞针不到位。处理方法:上模撞针回模时上模定位销不落时应调整撞针高度。
压脚错位。处理方法:待底模升至上模底面时调整压角,使其上下自如。
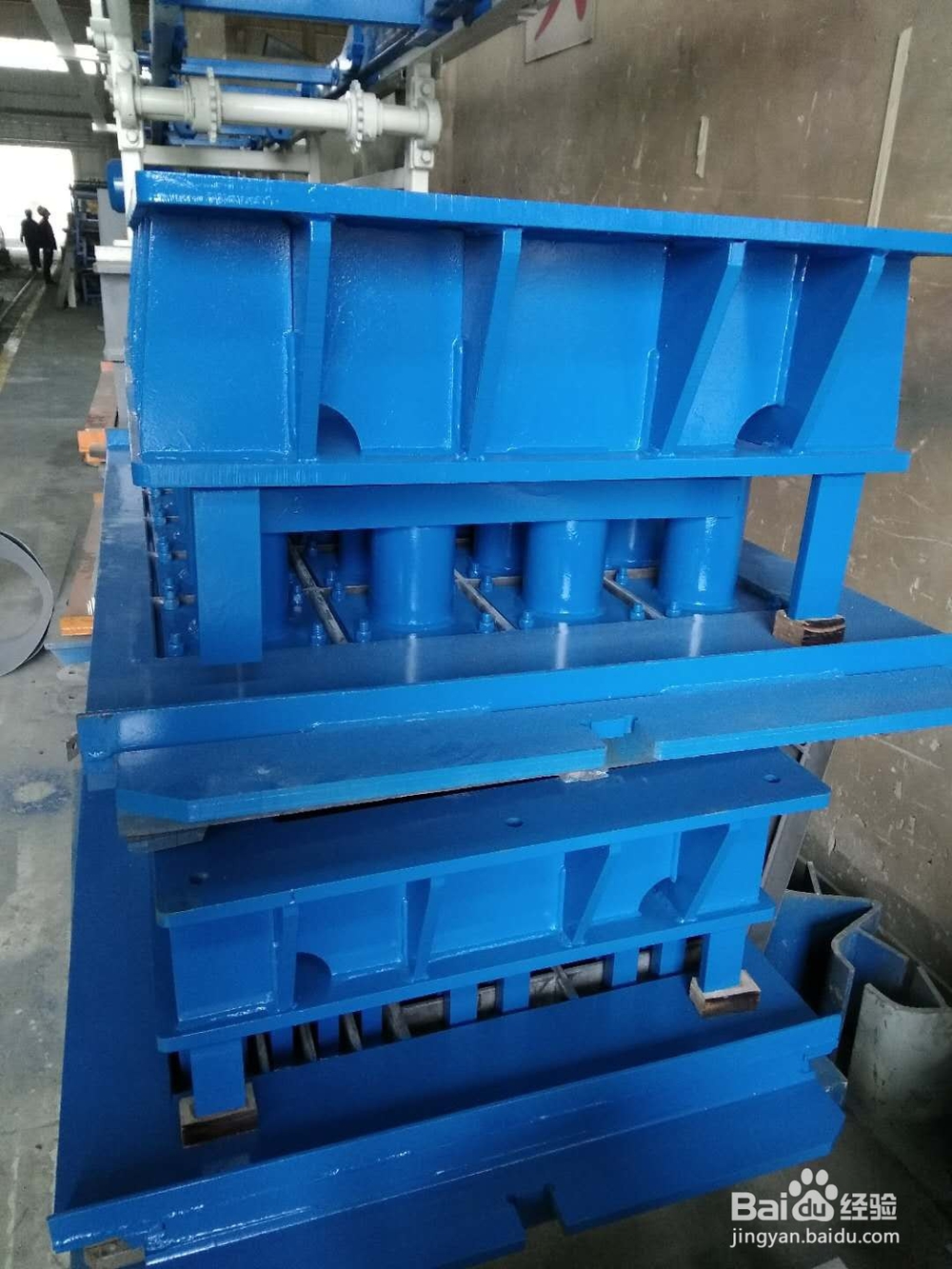
压力不足
故障分析:
底模压板缝过大。处理方法:如果压板缝过大可以将平台下面的弹簧加高所需高度,但加高不要超过5mm否则会影响传砖系统不能正常。
振动平台弹簧坏。处理方法:更换弹簧。
电机三角带松会使振动力不上底模。处理方法:调整电机三角带不应过紧。
下料不均匀原料没黏性及震动时间短时间都会使砌块压力不够。处理方法地方财政另有所指料和下料振动时间。
砌块高,处理方法:下调两侧定位板。

气顶坏密封圈
故障分析:
油杯在规定时间内用完,油号不按规定;处理方法:更换油及调整油杯顶针。
气顶偏顶。处理方法:待上模退回模后调整顶丝使跑道两侧间隙一样。

注意事项
安装模具时,使机口、芯具、机头中心与螺旋轴中心对正,否则将造成坯条烂角、弯曲等弊病;应检查芯头位置是否正确,芯头端面是否平齐,一般要求芯头端面回缩机口内1~2mm。
开机时的泥料软一些,当坯料进入芯具坯条成型情况良好后,调整坯料成型水分直至坯条软硬合适;成型时,要经常对泥条挤出速度是否平衡进行检查,检查的方法是把机口处外露的泥条切断,切齐,然后套上按等距离排好的钢丝网,开机挤出100~200mm泥条,停机测量被窑炉分割开的小泥条长度是否一致,从中可看出速度快慢的部位,以便及时进行调整。一般来讲海绵砖的四角泥料稍快些,这是因为四角摩擦阻力大,往往容易发生角裂等毛病。
在制品成型过程中,控制坯料走速的快慢,还可采用调整芯头的方法来调整,出料较快的部分可将邻近芯头调进,如四角出泥速度较慢时,则可将周边邻近四角的芯头稍微调出,如上述不能解决问题,则应在机口和芯具的结构上找出问题。
若泥料挤不出来,或局部走泥量少时,应停机查找原因,以免损坏海绵砖机设备;严格控制原料中内燃料的粒度,内燃粒度应小于3毫米。

砖机振动器的振动力不足,出砖周期长或出砖松密实度低,原因是制砖机下模下压的压力调节过大;,压力抑制了振动器的振捣,应将下托模油缸上油管对应的独自调压阀压力逐渐调小,直至制砖机的振动力正常。
自动制砖设备版权声明:
1、本文系转载,版权归原作者所有,旨在传递信息,不代表看本站的观点和立场。
2、本站仅提供信息发布平台,不承担相关法律责任。
3、若侵犯您的版权或隐私,请联系本站管理员删除。
4、文章链接:http://www.1haoku.cn/art_1170301.html